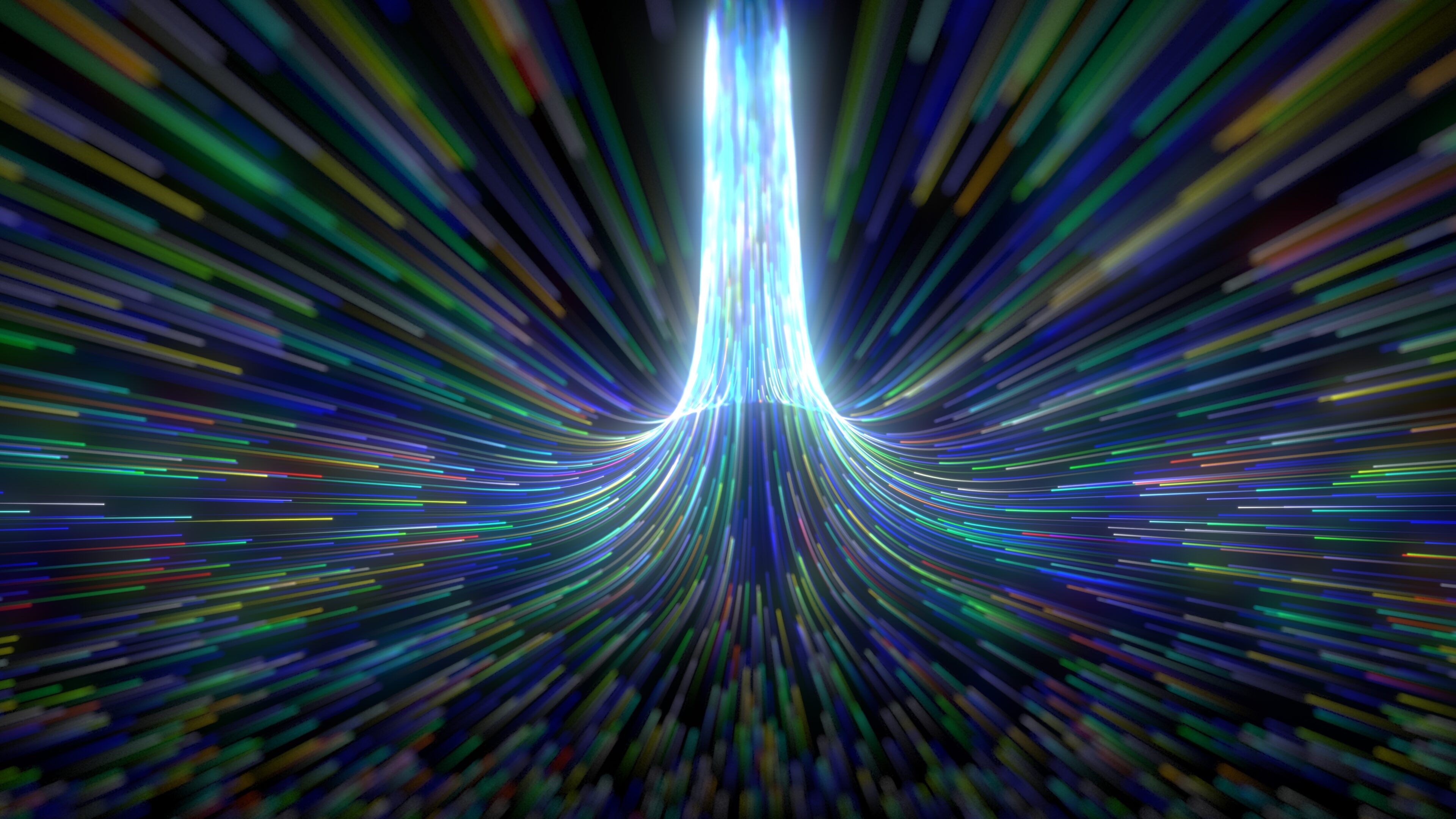
The Dark Magic of Fusion Control Systems
Fusion is the promise of a clean, unlimited–fuel and low–risk energy source of the future. In recent years, the pursuit of fusion energy has transitioned from a solely scientific challenge to a commercially attractive goal, thanks to the rise of innovative startup companies. The global need for a sustainable, carbon-free energy source has given these companies a key role in pushing towards commodifying compact fusion reactors designed for industrial power plants.
Fusion is hard
Decades of fusion research are culminating in the ITER project and other similar multi-party and national programmes around the world. Following painstakingly detailed roadmaps, a lot of knowledge has been gathered in academic institutions.
Namely, fusion is difficult to achieve and regulating all the necessary conditions for it is much more laborious than controlling fission in conventional nuclear power plants.
Managing the complex dynamics of plasma behaviour in sustained-fusion reactions — or attempting to impact small targets with synchronised high-powered laser beams (or any other fusion approach) — and simultaneously achieving stability, efficiency, and safety requires close coordination of real-time data processing, predictive modelling, and rapid response mechanisms. Only well-tested and mature control technologies can consistently provide fast, synchronised adjustments in response to dynamic and complex fusion processes, all in a big machine.
Fusion companies rock
The emerging private fusion sector is vibrant with entrepreneurship and startup mentality and has fostered a renaissance in the field.
Private–public collaboration is gaining importance as current private efforts try to leverage lessons learnt from past and current scientific fusion projects, building on their vast knowledge and experience. The new industrial wave of projects is underlining the challenges of quality, scalability, maintainability, and time-to-market – how to perform “lean and fast“.
Significance of the control system
The control system (CS) is critical to a fusion plant as it is its nerve-centre and brain.
Methods of fusion
There are various approaches to fusion (magnetic confinement, inertial confinement and others), and they all have some specific challenges from the perspective of a control system. However, from an elevated view, the main problems are pretty similar. The CS must provide precise, real-time control over variables and handle redundant systems, rigorous safety protocols, and intelligent error-handling mechanisms embedded within the control architecture.
The interface to all
The control system is the nerve centre of a fusion plant and presents the interface to all its subsystems. It is also, simply put, the structure that gives the operators and scientists the means to observe and regulate the machine.
Complex heating structures, containment with super-conducting magnets, fast repetition rates of consecutive shots and diagnostic systems, capable of capturing fast plasma changes – all are engineering challenges far from trivial.
The control system must, therefore, take into consideration the following considerations:
- The extensive size of the system;
- Unclear requirements of a FOAK (First Of A Kind) system due to the inherent R&D nature of the project;
- The expected (demanded) high performance;
- A consistent and straightforward interface for the user;
- De-facto functional integration of the whole machine (achieved through the control system);
- The necessity of facilitating long-term system viability (long-term maintainability and upgradability of system);
- Contesting consistent underestimation of CS complexity, development time, and budget.
FOAKs everywhere
All the commercial fusion projects are at the moment FOAK (or even a stepping stone towards a FOAK), with a comprehensive amount of R&D being done for the first time. This means requirements are inherently unclear and changing throughout the project — for some subsystems more than others. A direct result is that operation procedures are not fully understood during the design stage, but later.
Considering plant dimensions
A crucial determinant is the size of the fusion plant, taking into account subsequent planned prototypes and the demands for re-use. Growth in dimensions calls for substantial scalability that includes both a rise in signals‘ number and control loops.
The projected growth of the fusion plant requires a highly distributed and scalable control system with high-speed and robust data exchange. Therefore, it must also integrate high-speed communication, robust fault tolerance, and scalability to accommodate both experimental and operational demands of the fusion process. But that is not where the challenges end because commercial fusion systems also gather complexity as they “grow in scale“ –– until they increase to full reactor size.
Real-time controls are the name of the game
Fusion requires many real-time features, such as synchronising all actions and several feedback loops, either plasma control or target tracking or similar, which brings high–performance requirements.
Only well-tested control technologies can consistently provide fast, real-time adjustments in response to dynamic and complex fusion processes. Exact synchronisation – even in the femtosecond range – is demanded by some laser systems.
Data acquisition – a must for analysis
During the initial stages of the project, when the development team is still learning what is going on, it must nevertheless set the fundamentals for data acquisition. At a bare minimum, data must also be very accurately timestamped over several CS nodes so it can be correlated during analysis and easily retrievable.
Plant protection
Even though fusion reactors are not nuclear facilities (ITER excluded), there will still be a need to protect their personnel and environment as well as protecting the their large investment.
This requires redundant systems, rigorous safety protocols, and intelligent error-handling mechanisms embedded within the control architecture.
An additional layer of intricateness to the reactor is added by machine protection systems that typically need swift reaction times, faster than a slow–speed PLC-based interlock system can achieve. A layered control system architecture, where local control is combined with higher-level supervisory control, allows for quick, localised responses to issues — and overarching system-wide coordination.
Importance of control system design
A fusion reactor is functionally integrated through the control system. The parts, including local controls, usually come from several suppliers. A good approach to integration (including managing suppliers) starts with control system design and significantly affects problems during machine integration and commissioning.
Fusion projects take years
Projects are long-lived. It takes years to build them and many more years to operate them. The project team must address evolution and obsolescence management with care.
Design decisions are a balancing act
Every development stage (plant prototype) can be considered an individual project. There is a balance to be struck between time-to-market and not being overblown with design (needs are defined by the funding cycle) and the long-term wishes for re-use (avoiding throwing away too many things) with the overall goal of lowering the lifetime cost of projects.
Addressing the control system in a timely manner
The control system of a commercial fusion device is often underestimated. It may not pose a cryptic problem, but it is still very complex and its design impacts integration, safety, efficiency and upgradeability well into the project’s future. If it is addressed too late, it can jeopardise the project’s timeline.
The control system is the interface to all
Smart architecture is king
A well-thought architecture is needed to address technical and project requirements. One way to develop functional requirements of the control system is to collect use cases and system workflows as we analyse both operational processes as well as various testing or maintenance procedures.
Basic demands on the architecture
The control system architecture must be capable of supporting:
- diverse use cases and workflows;
- scaling to handle many signals;
- real-time performance and responsiveness;
- precise timing and synchronisation;
- safety and protection;
- appropriate hardware and software platforms;
- network topologies, cyber security;
- Integration, configuration management;
- data management;
- adoption of emerging technologies such as AI/ML, digital twins, and uncertainty quantification (UQ);
Real time requirements
One way to view the control system is to examine its aspect as a timing system in charge of clock synchronisation and trigger distribution. In this way, the CS is the orchestra conductor that makes all the instruments play in a harmonious manner. Clock synchronisation is important for timestamping data from the fusion device as operators and scientists must be able to correlate measurements to determine what is happening. Timing systems in big physics (e.g. public fusion projects) are usually of nano-second accuracy. For laser systems, it is common practice to treat the even faster synchronisation with a special femto-second timing system which is integrated with the overall machine timing.
The other part are real-time feedback loops that take data from one part of the machine (e.g. diagnostics systems), employ specific algorithms and feed results into actuators (e.g. magnet control). The speed of fusion processes requires such loops to be of the order of 1kHz or faster. (The challenge of inertial fusion will be the targeting system – one must be able to strike the fuel pellet accurately while it is being shot into the machine).
Scaling
Fusion control systems are composed of several tens — or even hundreds – of thousand physical signals. It is not uncommon that the number of signals rises as the project progresses. This can happen, for instance, when a whole new subystem (e.g. a particular diagnostics) is added to the system. The control system must handle it without changing its overall architecture in the next prototype.
Choosing HW and SW
There are many criteria for selecting hardware and software platforms and network topology, ranging from technical requirements and technology roadmaps (e.g., how long a hardware or software platform will be supported) to expertise availability (are universities still teaching young engineers this?).
Safety and protection
Protection and safety demands following safety-related standards, which are often country-specific. It is well-advised that the architecture detaches these functions from conventional control so they can be analysed (and possibly certified) separately.
Configuration management
Good integration capabilities that allow for incremental build of the plant and different configurations based on various use cases (type of »shots«, type of maintenance mode) are a must. The control system must be as configurable as we can afford to make it.
Data management
Data management is a topic on its own. Storing the machine data is just one aspect; retrieval must also be considered. Data provides knowledge not only of scientific processes but also of machine behaviour.
Support of emerging technologies
Emerging technologies (e.g. AI/ML, digital twins) are a promise to help accelerate fusion development. The challenge is how to integrate tools and approaches into the live control system, preferably in a standardised way so that developments can be shared over different projects.
A fusion control system is not a commodity
Fusion control systems pose a unique challenge compared to other industries. The public projects are well aware of this and have decades of experience. Today, it is impossible to buy a bespoke control system as a commodity that meets all the challenges of commercial fusion. From our experience over the years and across many projects in a tough technological market, the control system in complex, high-energy machines is often underestimated, leading to costly and avoidable issues down the line.
Table by Adam Stephen, Head of Advanced Control in the UKAEA Computing Division.
Some of the key risks
• Overlooking critical components: Certain control system elements may not seem crucial in the early stages but can later become bottlenecks or sources of system instability.
• Inflexible architecture: Poorly designed control systems lack necessary scalability or fast enough interfaces, making future adaptations prohibitively expensive.
• Technology obsolescence: Choosing rare or niche technologies can lead to long-term maintenance, management, and outdatedness challenges.
• Familiarity bias: Teams may opt for solutions with which they are comfortable instead for those that are best suited to the project’s needs, leading to inefficiencies and higher costs down the project road. To mitigate these risks, teams must lean into a deep understanding of all aspects of fusion control system and prioritise flexibility, scalability, and long-term maintainability when designing and selecting control system components.
Build or buy the control system? Both!
A crucial decision in control system development is whether to build the system in-house or procure a solution from external vendors. In reality, the best approach is often a balanced, hybrid one—combining both in-house development and external purchases.
The project team should, at the minimum, own the control system throughout the project, which means that its members must understand (including the reasons) the specifications and architecture and accept results.
However, not all aspects need to be developed internally. Partnering with external specialists for specific components can save a lot of time and resources while ensuring high-quality results.
The design and requirements phase should incorporate external expertise where needed, ensuring a comprehensive approach from the outset – that all the crucial questions are asked at the right time.
By leveraging internal expertise and external capabilities, projects can achieve a balance between control, innovation, and efficiency. Control system development is a particular engineering discipline in itself.
Work Breakdown Structures
A project plan is vital. In practice, the control system is often represented by just one line on the project Gantt chart, which does not describe the development status well enough to the project management.
One of the most common pitfalls in developing control systems for commercial fusion reactors is the lack of a sufficiently detailed project plan. Many projects suffer from weak Work Breakdown Structures (WBSs), which makes it challenging to track progress effectively. A well-structured plan ensures that each milestone is clearly defined and that engineers can systematically report their progress.
A robust planning approach should, therefore, include:
• A detailed enough WBS that breaks down the project into manageable components;
• A milestone-driven approach to track development progress;
• A framework that enables engineers to react to any specification changes fast and in an organised manner.
By establishing a well-organised roadmap, teams can avoid misalignment, delays, and inefficiencies that could otherwise derail the project.
First, ask, then plan
Before diving into development, it is essential for the project management/company decision-makers to ask themselves the right questions to guide the planning process:
1 When do we involve external specialists for control system development? ASAP, but at the latest, when the project is funded and starts. Engaging partner experts early can prevent costly re-work and design flaws later.
2 Who is a good fit for a partner? Someone who can ask the essential questions and knows what to do with the answers — in other words, someone who recognises how the answers affect the architecture and the plan. Selecting the right technology and development partners ensures seamless integration and long-term reliability.
3 What part of development should be kept in-house? Certain aspects, such as core intellectual property or highly specific system functionalities, may need to remain under the direct project control of the client. At the bare minimum, ownership should stay in-house, such as employees who will help provide needed information and understand the requirements (also reasons for them), understand architecture and be able to accept development (from various sources).
These answers help in structuring a roadmap that is both pragmatic and strategically sound.
(To be continued with blog part II – “Towards industrialisation of fusion control systems“.)
ABOUT THE AUTHOR
Rok Šabjan is a co-founder of Cosylab with over 25 years of experience in particle accelerator and fusion control system engineering. He currently serves as Deputy COO and Head of Fusion Business Development.
(To be continued with blog part II - "Towards industrialisation of fusion control systems".)