Reliable Laser Communications Between Space and Ground
Why Use Laser Communications in Space?
Harshraj Raiji spotlights the benefits of laser communication compared to RF (radio frequency) communication.
Laser communication (LC) can pack data onto tighter waves, which means higher bandwidth, allowing more data to be transmitted over a single link. While the achieved data rates depend on the signal-encoding scheme, among other things, in general, they could be 100 to 1000 times higher than rates in RF communication.
The electromagnetic beam divergence is directly proportional to its wavelength for a fixed aperture diameter. A shorter wavelength means reduced beam spread, and the resulting narrow beam increases intensity at the receiver for fixed transmitter power.
Because of their high directionality, optical links are more secure and less prone to interception, jamming and eavesdropping than radio frequency communication.
Furthermore, RF systems can experience interference from adjacent carriers due to spectrum congestion. Spectrum licensing has to be overseen by regulatory authorities, such as the ITU (International Telecommunication Union). On the other hand, optical systems are still exempt from spectrum licensing, reducing the initial set-up cost and development time.
The new Field of Ground-to-Sat Communications
While two-way laser communication between vehicles in space is already a well-tested solution over millions of kilometres, LC high-throughput links through Earth’s atmosphere can quickly become problematic at distances of even a few kilometres.
Miha Vitorovic emphasises that there are many reasons for LC not performing optimally, including rain, snow, fog and weather in general – and scintillation, wind-affected pointing stability and pollution.
For instance, to minimise the effects of pollution and background noise, some Optical Ground Stations (OGSs) can be constructed in very remote locations, which present new challenges. Most of the latter are connected to logistics – building an OGS at a remote location and bringing in electricity and high-bandwidth data communication. Of course, once the OGS is deployed, it also has to enable access by maintenance crews. If it is remote, we can be exposed to high costs, difficult access and other problems. We would want to minimise the involvement of the maintenance crew as much as possible.
But even remote locations cannot avoid the problem of cloud cover over a wider geographical area. One of the solutions is to have a network of optical ground stations in dispersed locations or have an RF link as a communications fallback.
Is Laser Communication a substitute for RF Communication?
As a business insider, Daniel Hendrix answers whether laser communication will ever replace RF links. Although LC has a lot of potentials, it will never fully replace radio frequency communication in the ground segment, as they are two very different things. There are, of course, many advantages to optical comms, but RF retains features that make it irreplaceable inside the atmosphere.
For example, planners must consider cloud cover and the proper sites for optical ground stations. Furthermore, to replace RF ground stations with OGSs, you have to do this one on one, employing a different business model than with RF – which is a challenge for the industry.
Airbus has been busy with the mentioned optical comms issue for years, starting initially in the space segment space with its Space Data Highway (SDH), a public-private partnership between ESA (European Space Agency) and Airbus. SDH is a European Data Relay System (EDRS) laser communication infrastructure that delivers high-bandwidth data transfer to airborne nodes and Low-Earth-Orbit (LEO) satellites. Airbus is now moving forward to develop ground-based capabilities for laser communications.
Free-space optical (FSO) communication is, in short, technology that uses photons moving in free space – air, vacuum or outer space – to wirelessly transmit optically -encoded digital data. Olivier Jacques-Sermet sees we have reached the inflexion point where “all planets are starting to align”, favouring laser communications.
If we look back 25 years, when the first commercial use of laser-comms started, nothing much had happened due to significant technical limitations and lack of market readiness. But in the last five years, we have witnessed a strong acceleration in technological advances, the emergence of real-life use-cases for both civilian and sovereign or defence applications, and a solid stream of venture capital money ready to support investment in the new laser-comms infrastructure.
Technical overview of Optical Ground Stations
An infrastructure of a network of optical ground stations is needed to enable seamless and worldwide coverage of optical satellite-to-ground communications. Harshraj Raiji explains what subsystems should be in an OGS.
On the downlink, an optical ground station has to collect photons with a telescope and focus them onto a detector, where the light is converted into electrical signals. These are then processed to recover the information embedded in the beam. But OGS is much more than just a “telescope with a detector”.
We also need a dedicated pointing acquisition and tracking subsystem which contains sensors and electronics to steer and control the active elements of the optical bench assembly (like fast steering mirrors) in a closed loop, pointing the laser towards the target terminal. It must acquire a signal and track it continuously during the uplink/ downlink phase.
Another subsystem controls and monitors the principal parameters, such as wavelength and power, of the transmitted laser beam. And of course, we need a dedicated signal characterisation subsystem for both the received and transmitted beam that includes, among others, BER (bit error rate) analysers, polarimeters, spectrometers and wavefront sensors.
Last but not least, Harshraj underlines OGS also has to interface with various external systems, including meteorological stations and network subsystems, especially when the latter is part of a more extensive network of ground stations. The OGS must also know the target satellite orbital elements and trajectory, so it should “know how to talk smoothly” to a satellite control centre or mission-planning system.
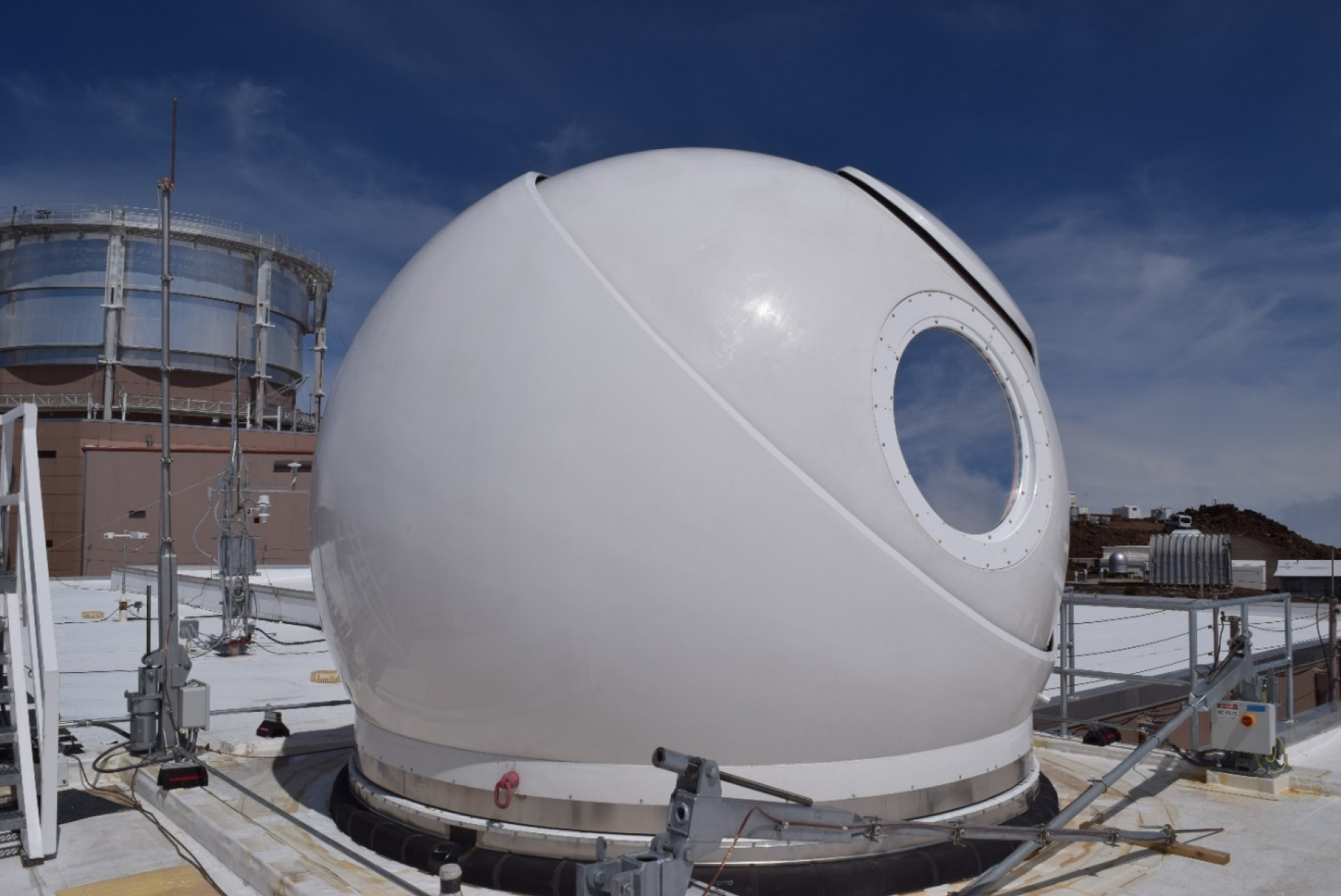
The Optical Chain of Ground Stations
When an optical signal crosses atmospheric turbulence, it will suffer from many issues that disturb the signal, like beam wandering, defocus, and scintillation. These may even prevent the beam from being adequately focused on the detector. That is why, explains Olivier Jacques-Sermet, mitigating atmospheric turbulence is still a challenge.
Without compensation, we have to utilise large and slow detectors limited to low data rates, preventing realising the full potential of optical communication. We may suffer from higher BER in strong turbulence conditions, demanding frequent retransmission – or even complete signal loss. So, it’s critical to mitigate the effects with various solutions.
One way is to use adaptive optics, which measure phase distortions and correct them with a deformable mirror. We can also employ innovative and scalable solutions based on spatial demultiplexing and optical recombining, much more suited to large-scale optical ground-station deployment.
The Control System for OGS
Miha Vitorovic points out that all OGS subsystems must work together correctly and reliably. Concerning systems software, he sees that we have two significant dimensions at play at OGS.
One is telecommunications, so we need to quickly and reliably transfer data between the optical ground station and where it’s needed. The second is that many subsystems in an OGS work in parallel and must be supervised and controlled. For precisely this purpose, they are similar to distributed control systems with which Cosylab has experience in countless other projects is ideally suited.
Such systems enable the reliable control of some of mankind’s most famous scientific experiments and proton therapy devices. These are complex systems with many moving parts and a multitude of devices and interfaces that need to be integrated.
These systems also have to conform to stringent performance and throughput requirements since a lot of data has to be processed and archived. They demand long uptimes because unscheduled downtime always costs money. And in the instance of the medical therapy machines, downtime can literally cost lives.
Miha sees that Fault Detection, Isolation and Recovery (FDIR) must be automated as much as possible, so the systems work with the least human intervention possible. And this holds true either for the accelerators where safe irradiation of patients is the goal or in the optical ground systems where it’s not feasible always to have a crew ready to visit the remote location for unscheduled troubleshooting and maintenance.
How to Guarantee OGS Uptime?
Complex systems can also be quite fragile and expensive to maintain.
Daniel Hendrix draws attention to the importance of remote management and control software. In his opinion, complexity is always translated into cost, making complexity expensive. The solution is to implement software that enables optical ground stations to be competitive instead of seeking results from the existing state of the art.
Having widely dispersed OGSs demands tight control on maintenance; otherwise, operating expenditures can go through the roof, impacting the end customers. As this has to be avoided at all costs, deploying the right control system for optical ground stations’ automated operations is fundamental. Daniel Hendrix sees the adoption phase of free-space optical communication preceding large-scale use in the mid-term. Namely, engineering teams must first ensure reliability and uptime. It was relatively easier to put the current optical system in place for inter-satellite communications.
Once all the engineering challenges for OGS have been overcome, Airbus NL is ready to produce a competitive product for the space market. The result will be an end-to-end solution, embracing OGS equipment, airborne terminals and the control software, which is key to keeping costs low.
Airbus NL is steadily preparing the development requirements for high-bandwidth and reliable OGS terminals, focusing on the technology, managing the future supply chain, and mastering industrialisation. The company is working with relevant partners to position itself – in alignment with other Airbus entities – to be ready to scale up when the time comes. It is precisely for this reason Airbus is also partnering with Cosylab as one of its industrialisation partners.
The adoption of Large-scale Use of laser communications
Harhsraj Raiji believes that the technology must become proven and cost-effective both at the ground station and onboard the satellite for laser communications to become commercially available.
Satellite and ground operators should adopt collaborative approaches for R&D and, later, for operations; lessons learned should feed back into the design and refinement of operational concepts of the ground and space segments. The OGS network must be diversified to increase downlink opportunities to mitigate meteorological disturbances. More work needs to be done on the ground infrastructure to automate OGS operations and render these ground stations cost-effective.
An excellent way to render these OGSs cost-effective would be to build the software parallel with the hardware. Cosylab has repeatedly witnessed projects where customers underestimated complexities on the software side. Most of the problems were discovered only very late because most of the R&D time went first to hardware subprojects. This means that in the final phase, when software is integrated and refined, many problems often pop up, in the most critical time.
The Future of Optical Ground Stations
What would it take for the technology of free-space optical communication to be used broadly in our everyday lives? Olivier Jacques-Sermet from Cailabs explains from the viewpoint of a deep-tech hardware company, expert in light-shaping solutions using patented technology.
The key in successfully transitioning laser communication from a trending research topic to operational use-cases and profitable business cases is to get the whole supply chain ready for production and scale-up. This is true for New Space startups and SMEs and for legacy prime contractors, who need to work together in good intelligence and transparency so that all the subsystems can work together and address upcoming projects most fruitfully.
Daniel Hendrix from Airbus (ADS NL) notes that the FSO domain development is picking up speed. The market for quantum key distribution (QKD) is growing, and Airbus is partnering with several companies throughout Europe to realise its potential.
Possibilities are opening for entering the domain of optical feeder links for direct Earth-to-LEO data communications with satellite constellations. Airborne applications also seem to be becoming more and more commercially attractive. Airbus is now working on a unified roadmap regarding FSO, defining the roles of all cooperating entities and optimising development efforts to offer end-to-end solutions in a timely fashion.
Miha Vitorovic concludes the debate by confirming that Cosylab supports Airbus with its software expertise in control systems, integration of disparate and “exotic” hardware, experience in creating operator interfaces (screens), and supporting services like archiving and logging and configuration. The company is already collaborating with ESA on its release of the EGS-CC – a common control system that will be used for all of Europe’s ground segment needs – and as such will play an essential role for the OGS segment in the future.
ABOUT THE PANELLISTS AND THEIR COMPANIES
Daniel Hendrix is a business development manager in laser communications from Airbus Defence & Space Dutch Technology (ADS NL) in Leiden, the Netherlands, and an aerospace engineering graduate from the Delft University of Technology.
Olivier Jacques-Sermet is a sales and business-development manager of laser communication solutions from Cailabs, a French company headquartered in Rennes. Olivier is an optical engineer with more than 15 years in deep-tech photonics.
Miha Vitorovic is the head of the space engineering department at Cosylab and a computer science graduate with many years of control-systems experience.
Harhsraj Raiji is a mechanical and space engineer with past experience as a mission analyst and a system engineer on various industrial and space missions. At Cosylab, he is part of the Space team, acting as a project manager, team leader and business developer.