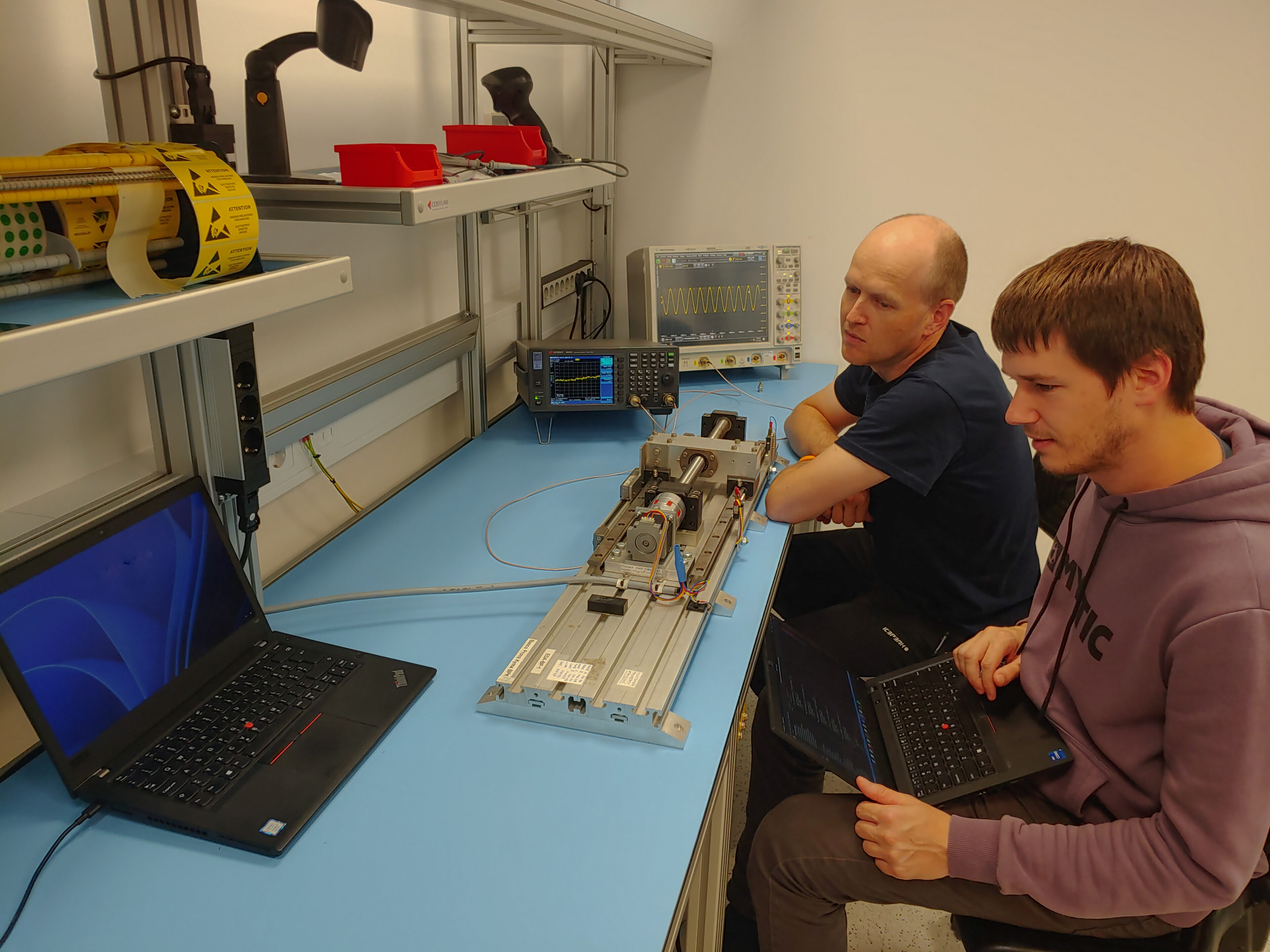
Upgrading an X-ray Interference Lithography System and Perfectly Replacing Motion Control
We are used to aiding clients overcome these challenges so they can modernise safely, efficiently and within deadlines. We perform system refurbishment by applying the right mix of structured and agile software engineering to address challenges arising with each innovation process cycle.
For semiconductor equipment manufacturers, such as providers of lithography systems and their components, we can streamline complex system deployments and integrate various functional solutions, such as motion systems of various complexities. One such case is our work at the lithography station of PSI.
The Paul Scherrer Institute, or PSI, is the principal Swiss multidisciplinary engineering and natural sciences research institute. PSI’s Laboratory for X-ray Nanoscience and Technologies (LXN) performs EUV Interference Lithography experiments with their XIL-II End Station being able to break the record in six-nanometre EUV-IL resolution in the past.
Cosylab has decades of experience in control systems and subsystem integration for complex machines. As such, we were a natural choice for the PSI’s ALM (Advanced Lithography and Metrology) group to help them integrate a new motion control system and machine protection system (MPS) for its XIL-II End Station.
Challenges | Solutions | Results |
|
|
|
“One of the challenging aspects of this project was the fact that none of the original XIL engineers were available for the specification gathering phase for the End Station, so we helped the LXN team formulate the specification requirements by going through initial conversations and interviews, how they are actually using the existing system day to day.
We worked together on the system engineering process, learning along the way all about the potential pitfalls and contingencies they had experienced in the 20 years of user experience with the End Station. It was one of our exciting cases of how to guide the customer with questioning and rechecking until we got to the final system requirements, which they confirmed.”
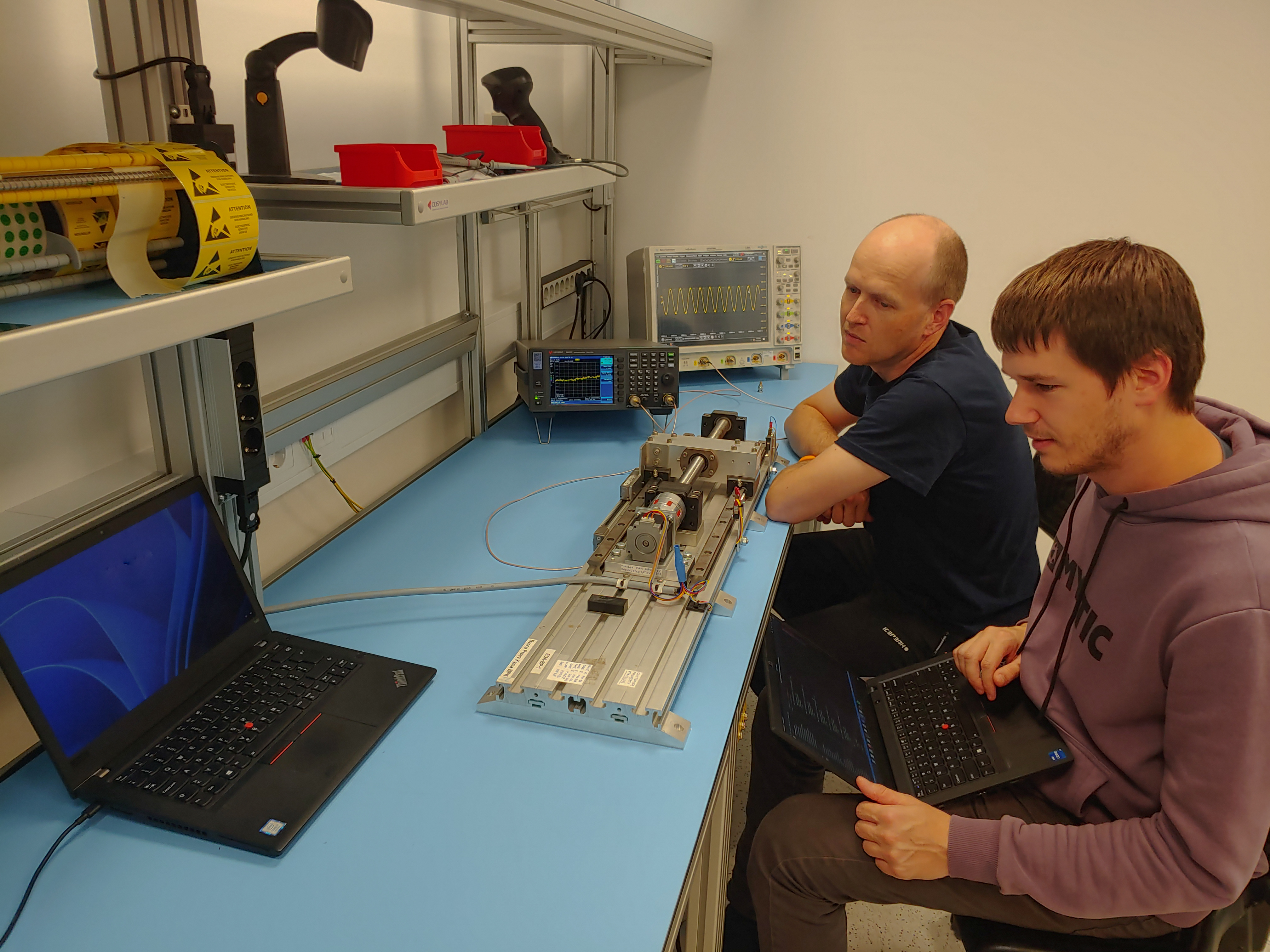
Three Main Challenges of the End Station Upgrade
“The Cosylab team we worked with was extremely professional. They delivered a high-quality job in a timely and transparent manner while meeting all deadlines."
The upgrade of the End Station included several substantial enhancements. The client decided to implement a novel protection system using a new PLC platform that also acts as an interface for all protected devices, including vacuum valves, gauges, and pumps.
Firstly, we found that most of the system could only be tested directly at the location of the End Station. However, we were able to remotely simulate the basic components of the machine protection system (MPS) by ensuring all functional inputs were correctly mapped to their outputs.
Secondly, configuring the motion control posed a more significant challenge, as it required on-site testing of the actual motors to ensure proper access and functionality. The third major hurdle involved ensuring the main state machine operated correctly. This machine coordinates all devices to execute the precise lithography exposure process at the End Station.
This process was complex due to its many components—some new, some old, and others that had to be redesigned. Integrating these parts to function harmoniously presented a significant challenge.
"We had a very good collaboration with the Cosylab team, both from a distance and on-site. They are very professional and come up with solutions on the fly!"
Engineering Flexibility as the Keystone of Integration
The End Station upgrade project commenced with an on-site meeting to review the machine, alongside weekly meetings involving both Cosylab and the client’s team. These sessions allowed us to outline our steps and gradually build a comprehensive understanding of the End Station system.
Through iterative question-and-answer sessions, we began constructing a mental model of the system, enabling us to test our assumptions in real time with our client. Although our focus was primarily on the motion controls and equipment protection system, it was essential for us to understand the entire End Station exposure system thoroughly. We were also tasked with redesigning the machine protection system (MPS) to accommodate a new PLC subsystem.
To enhance convenience for our client, we crafted an elegantly integrable hardware solution in the form of a black box. This comprehensive assembly included a PLC with its power supply unit, input-output cards, and a panel equipped with all necessary connectors for linking components to the PLC subsystem. Additionally, it incorporated a networking switch and a fuse assembly, all neatly housed within a standard rack form factor.
This deep dive into the system’s intricacies was necessary to effectively integrate the new motor controller and modify the system accordingly, essentially requiring us to reverse-engineer the existing setup. The result precisely replicated the functionality of the existing motion control with exactly the same accuracy.
Additionally, we reverse-engineered, then refactored and upgraded parts of the EPICS control system to incorporate the new motor controller into the End Station’s motion control assembly. This extensive reengineering and integration work was completed in only five months, with the final weeks spent on-site.
Although we did simulate the basic parts of our system upgrade beforehand, we performed most of the testing and resulting system modification during the short two-week commissioning and acceptance phase on-site at PSI.
"I would estimate that about two-thirds of our work involved system engineering. This primarily consisted of reverse-engineering the existing system and enhancing our understanding through iterative discussions with the client about how they use the machine. Once we had completed this foundational work to a high standard, the subsequent development phase was relatively smaller in scope. The commissioning and testing phases proceeded very smoothly, resulting in a highly satisfied client at the project's conclusion."
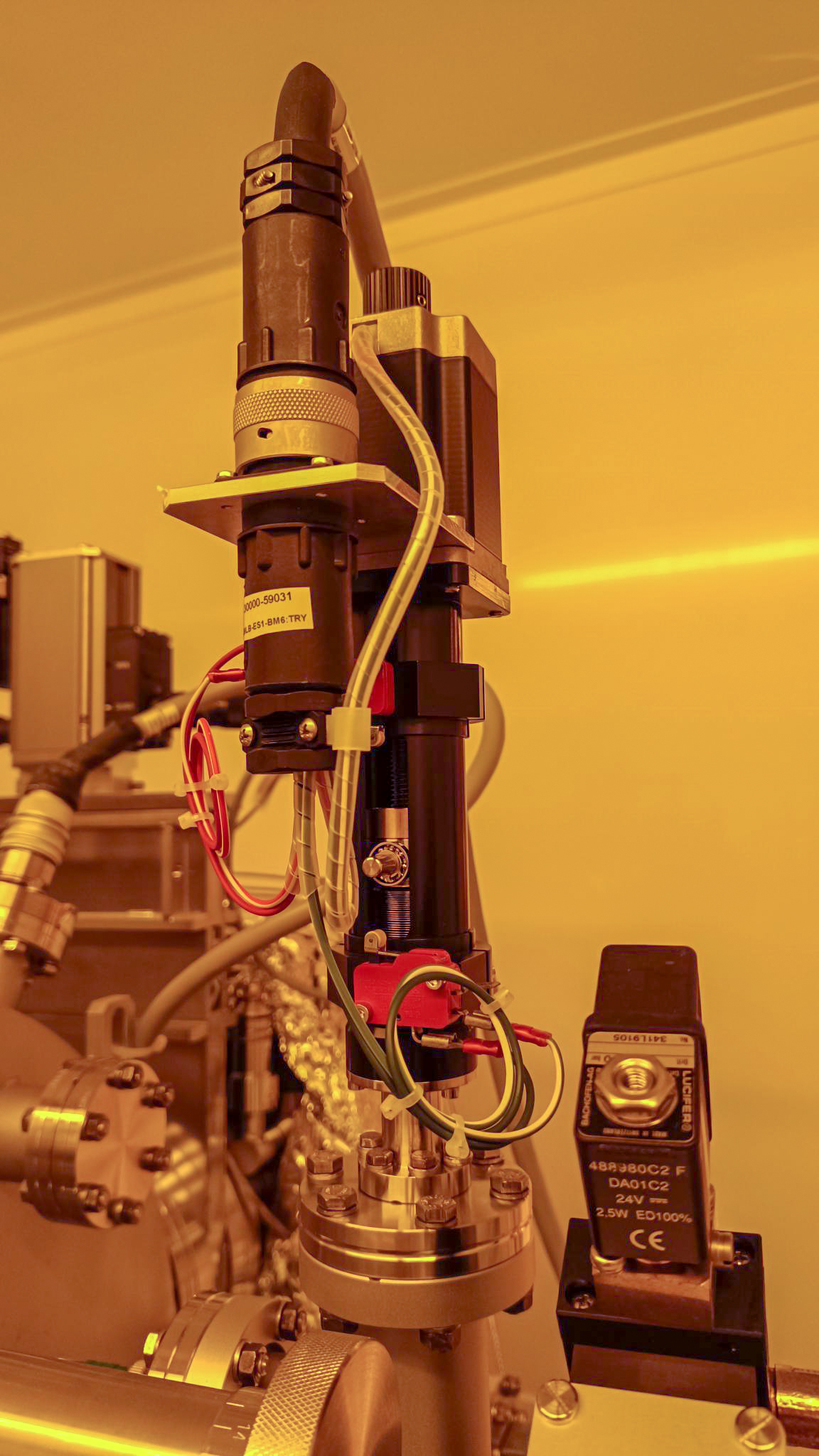
XIL-II End Station — How its Revamped Control System Works
The PSI’s XIL-II End Station is designed to create periodic nanostructures using EUV interference lithography. A coherent EUV beam illuminates a diffraction mask, and the interference from multiple diffraction orders generates a periodic pattern on the surface of a silicon wafer coated with a photosensitive material.
This exposure initiates chemical changes in the resist, vital for creating ultrafine structures necessary to manufacture microprocessors and memory devices.
The control system, working in tandem with the MPS, orchestrates the entire exposure process for the substrate sample. Initially, it verifies that the exposure chamber maintains the correct vacuum. At the same time, and before moving the mask into its correct position in the exposure chamber, the system also measures the beam flux, which is essential for calculating the proper dose.
Then, it manoeuvres the motor-driven assembly, correctly positioning the substrate wafer under the lithography mask and exposing the sample to the synchrotron’s light beam. The final step involves repositioning the sample for further processing.
All Objectives Achieved, Client’s End Station On-line
We were tasked by the PSI’s ALM group to refurbish two critical subsystems of its XIL-II End Station, MPS and motion, to maintain its existing functionality and ensure backward compatibility.
Cosylab assisted the client in defining the technical specifications and requirements and then entirely engineered the solution. Adopting an agile development methodology, we performed just-in-time testing directly on-site at the client’s lithography facility.
We started with a legacy integrated system and created a new modular and flexible main control system (CS) that includes an upgraded MPS and revised motion subsystem with integration for the new motor controller, both fully integrated with existing software and hardware. The new motion subsystem can reproduce precisely and with very high accuracy the motion that the old solution was providing.
Many companies want to upgrade their system, yet they often fear whether the new system will be as good as the old one. We have proven that it is indeed possible.
"We are thankful to Cosylab for the great work and rapid problem-solving on a tight schedule! The company really helped us formalise and document all of our system's logic, which was crucial for setting down our system upgrade requirements.
It was a pleasant experience for us, and in the last two weeks of testing and commissioning, we learnt a lot ourselves. Hopefully, we'll get the chance to collaborate with the company again."